
Ebenheitsbestimmung nach DIN 18202, DIN 15185
Präzise Messung zur Bauabnahme
Ist die hergestellte Fläche eben? Ist sie wellig? Ist sie geneigt?
Fragen, die Bauherren nach Fertigstellung von Bauteilen nicht nach Gefühl, sondern durch präzise Messung beantwortet haben wollen.
Dort ist das Messprinzip geregelt. Es beruht auf herkömmlichen Prüfmethoden mittels eines Richtscheites. Wird z.B. ein 2 m langes Richtscheit auf eine Fläche gelegt, so darf in der Mitte bei 1 m der Abstand von der Fläche zum Richtscheit ein bestimmtes Maß nicht überschreiten. Wie groß dieses Maß ist regelt die vom Bauherren mit dem Auftragnehmer abgesprochene Qualitätsstufe (z.B. „wie Zeile 3, jedoch mit erhöhten Anforderungen“).
Es ist jedoch nicht nur zu prüfen, wie sich die Fläche bei 1 m Messabständen verhält. Es ist ebenso entscheidend, ob auf 10 cm Längen (kurzwellige) Abweichungen auftreten oder ob z.B. auf 15 m (langwellige) Fehlereffekte in die Fläche eingebaut wurden.
Es sind also von 10 cm Messabstand bis 15 m Messabstand alle in der DIN aufgeführten Maße auf Einhaltung der Toleranzen zu prüfen. Theoretisch wird also die gesamte Fläche durch Verschieben von Richtscheiten in Längs- und Querrichtung auf diese Weise geprüft.
Nach DIN 18202 kann diese Messung auch durch ein Flächennivellement erfolgen. Zitat: „Beim Flächennivellement wird die Fläche durch ein Raster unterteilt, z.B. mit den Rasterlinienabständen von 10 cm, 50 cm, 1 m, 2 m usw. Auf den Rasterschnittpunkten werden die Messungen vorgenommen. Auswertung der Messergebnisse der Strecken 4 bis 6 an der Höhenkote Nr. 5, 5 bis 10 an der Höhenkote Nr. 7 usw.“
Die Erstellung und Einmessung des Rasters sind extrem aufwendig. Die Auswertung ist sehr umfangreich, da die im Nivellier gemessenen Höhen noch den Rasterkoordinaten über Punktnummern zugeordnet werden müssen.
Moderne und hochgenaue Messmethoden vereinen die Lage- und Höhenmessung, d.h. in einer Datenzeile werden 3D-Koordinaten jedes Messpunktes gespeichert. Eine gesonderte Zuordnung von Lage und Höhe über eine einzugebende Punktnummer entfällt.
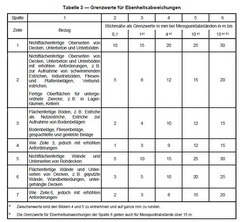
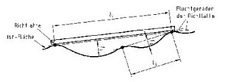
…liefert jedoch weiterhin Ergebnisse nach DIN 18202.
Je nach Qualitätsanforderung der Fläche kommen entweder Laserscanner für geringere Anforderungen oder der Lasertracker zum Einsatz.
Mit dem Scanner werden große Flächen automatisch erfasst. Das Messpunktraster liegt im Bereich unter 1 cm. Die geforderten Rasterpunkte in den genannten Abständen werden aus den jeweiligen Nachbarpunkten interpoliert.
Aufwendiger ist die Messung, wenn die höchsten Qualitätsanforderungen an den Boden gestellt werden. Hier dürfen bei einem Stichmaße von 10 cm nur Abweichungen von maximal 1 mm auftreten. Um diese Aussage gesichert treffen zu können, wird der Lasertracker mit einer Messgenauigkeit, die bei 1/10 mm liegt, eingesetzt.
In Linien wird automatisiert der Boden z.B. im 10 cm Abstand abgetastet. Theoretisch müssten die Linienabstände quer ebenso gewählt werden. In der Praxis werden in Querrichtung die Messabstände meist reduziert. Hier kann die Messung z.B. auf die typischen Fahrspuren (Reifenbreite und Achsbreite) von Fahrzeugen abgestimmt werden.
In der häuslichen Auswertung werden dann mit Hilfe von Exceldateien alle möglichen Linien und Linienabstände berechnet (siehe Zitat aus DIN oben). Dies geschieht sowohl in Längs- als auch in Querrichtung. In den Tabellen werden alle nach DIN erforderlichen und berechenbaren Kombinationen abgefragt. Messwerte innerhalb der Toleranz sind grün dargestellt, Abweichungen erhalten die rote Farbe.
Durch die Prüfung von verschiedenen „Richtscheitlängen“ in einer Tabelle, kann es vorkommen, dass Messpunkte z.B. bei den kurzwelligen Prüfungen (10 cm – 1 m) ohne Fehler sind, jedoch im langwelligen Bereich (>1 m) die Toleranzen nicht eingehalten werden oder umgekehrt.
In der Regel werden sich in den Tabellen „Bereiche“ herausbilden, in denen die Messwerte auch von benachbarten Punkten außerhalb der Toleranz liegen. In diesen Bereichen muss dann ggf. nachgearbeitet werden (siehe Auszug einer Tabelle rechts).
Zusätzlich werden die Messpunkte in einer Grafik eingezeichnet und farbig markiert. Ein Punkt, der in mindestens einer Tabelle als außerhalb der Toleranz liegend gekennzeichnet wurde, wird in der Grafik ebenfalls rot dargestellt. Alle anderen sind mit einem grünen Symbol versehen.
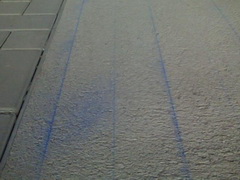
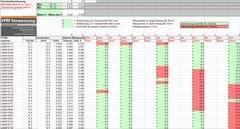
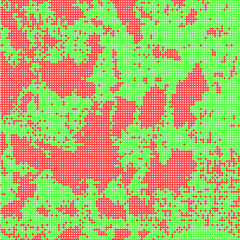
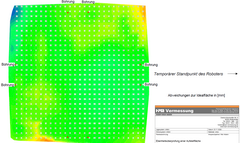
Besondere Bedingungen werden an Böden in Hochregallagern gestellt. In den schmalen Gängen zwischen den bis 15 m hohen Regalen fahren automatisierte Fahrzeuge. Bei unebenem Boden könnte eine leichte Querneigung das Anstoßen im oberen Bereich bedeuten. Welligkeiten in Längsrichtung können zum Aufschaukeln des Fahrzeuges führen.
Daher wurde die Richtlinie „Böden für den Einsatz von Schmalgang-Flurförderzeugen“ vom VDMA herausgebracht, die in Verbindung mit der DIN 15185 und der DIN 18202 die Ausführungsbestimmungen der Ebenheitsmessung regelt.
Grundlage hier ist ein Messwagen, der mit einer Messuhr versehen ist. Der Wagen hat die Breite einer Reifenbreite eines Förderers und weist drei Räder pro Achse auf. Dadurch werden Querneigungen im Querprofil der Reifenspur ausgeglichen. Während sechs Räder des festen Teils die Basis bilden, ist der vordere Teil um die Vorderachse beweglich. Da sich die Querneigung auf das Vorderteil überträgt, liegt mindestens ein Rad des beweglichen Vorderteils immer auf. Der Höhenunterschied zum starren Teil wird gemessen.
Hier wird als Resultat die Welligkeit der Bahn in der Längsrichtung als Maß für die Ebenheit bestimmt.
HPM hat den Messwagen nachgebaut und bestimmt die Lage des Messwagens und die Höhenänderungen mit Hilfe eines Lasertracker. So werden keine Höhenunterschiede, sondern direkt die Höhen des Vorderwagens gemessen und in die Auswertetabellen übernommen.
Die Welligkeitszahl wird kontinuierlich mit der Strecke berechnet und mit dem Grenzwert, der von der Förderhöhe abhängig ist, verglichen.
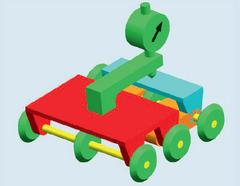
Quelle: VDMA Richtlinie „Böden für Schmalgang Förderzeuge“